Pioneer of the mixing column
Complete expertise in design and build of a mixing column
Mixing columns are designed for continuous operation and have a continuously operating plug-flow reactor that has recognised advantages: reduced costs and floor space, ease of operation, etc. The principle is to include in a column the equivalent of a cascade of J perfectly mixed reactors. The higher the number of mixed reactors, the more it resembles a plug-flow reactor. This number is defined according to the chemistry and the optimum economic investment.
In an industrial environment, two techniques can be used: perfectly mixed reactors and the column of J levels.
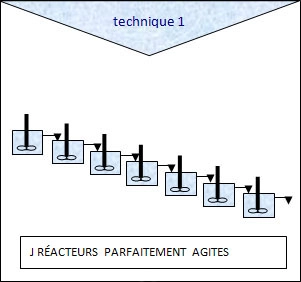
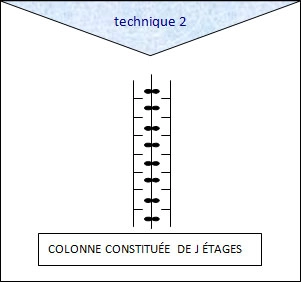
The advantages of mixing columns
Vertical concentration in a single machine drastically reduces instrumentation and transfer devices. A mixing column enables savings in investment, operating costs, maintenance and floor space. In addition, it is easy to use as there is only one piece of equipment to be driven and controlled.
The most common applications of mixing columns
- Liquid-liquid extraction: material transfer from an aqueous phase to an organic phase.
- Maturation: residence time is essential for the sizing. The particle residence time is simulated in the column, so that customers can calculate the “maturation” rate for their product.
- Reactions: depending on the speed of the reaction, the product conversion rate is calculated at each stage. A technical/economic calculation determines the optimum number of stages.
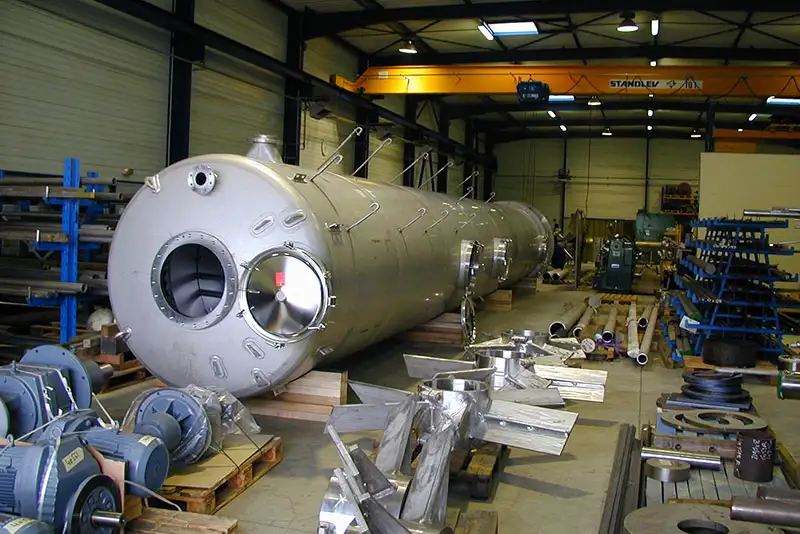
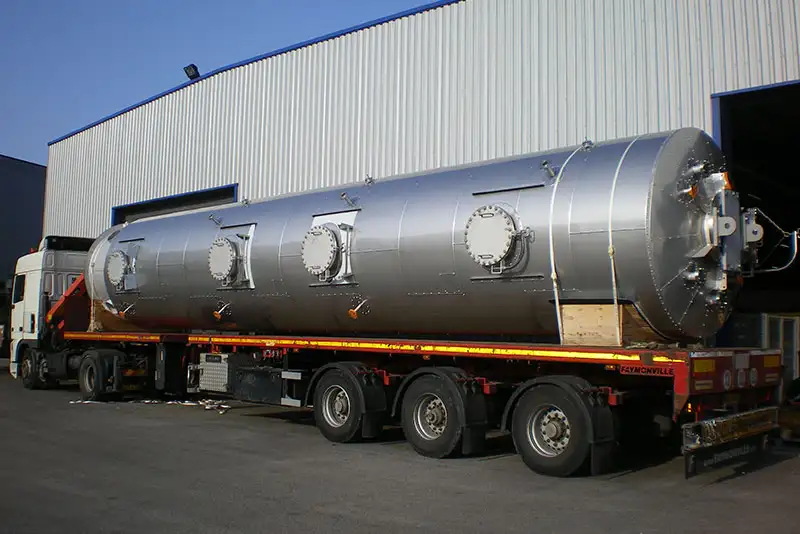
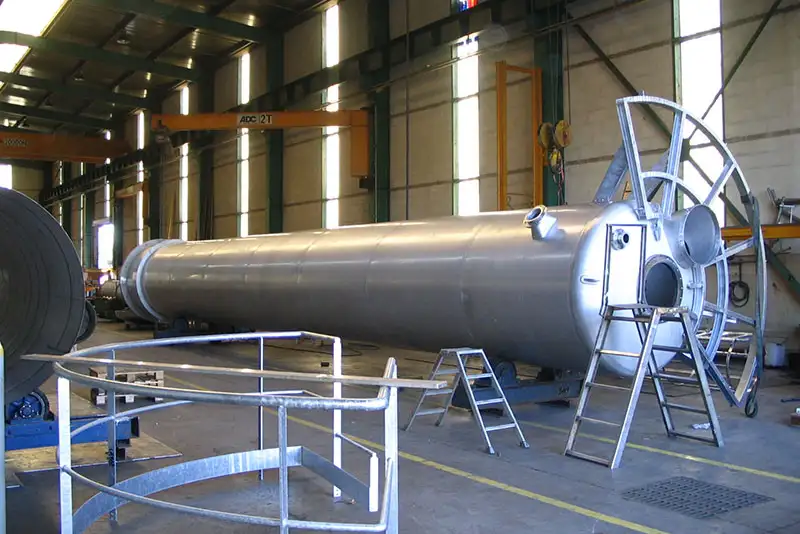